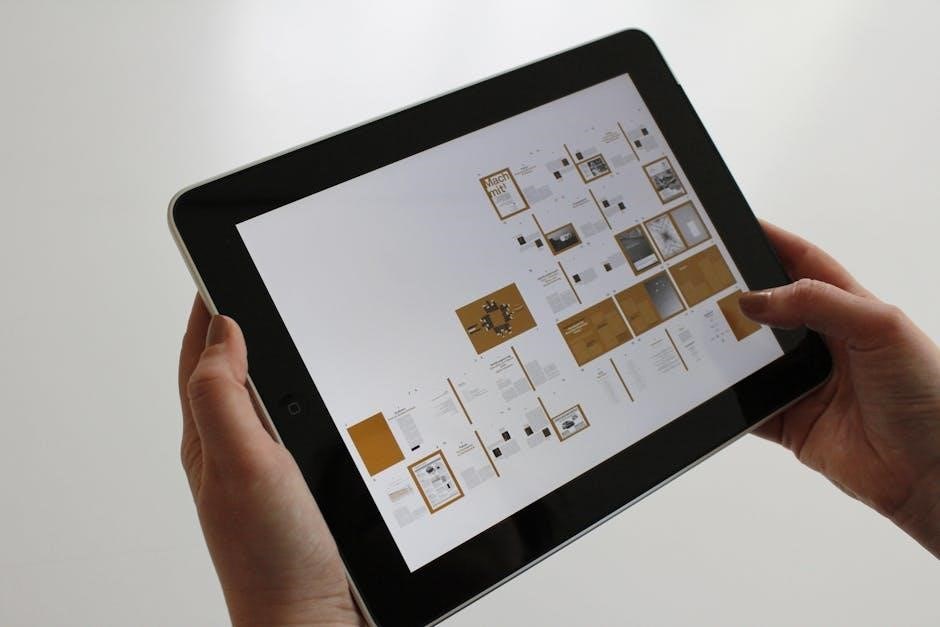
PowerFlex 525 User Manual: A Comprehensive Guide
This comprehensive guide serves as your portal to understanding the Allen-Bradley PowerFlex 525 adjustable frequency AC drive.
It offers essential instructions for operation, maintenance, and troubleshooting, ensuring optimal performance and safety.
The PowerFlex 525 is an adjustable frequency AC drive designed for motor control applications, part of Allen-Bradley’s versatile PowerFlex family. This drive offers a compact design with powerful performance capabilities, catering to a wide range of industrial needs. The PowerFlex 525 provides users with flexible motor control, easy integration into automation systems, and simplified commissioning.
This drive commonly works with Rockwell Automation controllers via EtherNet/IP networks. It also offers embedded EtherNet/IP adapter for streamlined communication and control. Within this user manual, you’ll find detailed instructions on how to install, configure, and troubleshoot your PowerFlex 525 drive.
Whether you are a seasoned professional or new to variable frequency drives, this guide aims to provide the knowledge and resources necessary to maximize the benefits of the PowerFlex 525 in your application. This user manual is designed to empower users to configure I/O messaging, set up adapters and implement direct run options.
Key Features and Benefits
The PowerFlex 525 adjustable frequency AC drive boasts several key features that make it a versatile solution. One of the most notable advantages is its compact size, which allows for installation in space-constrained environments, while not compromising on performance. Its embedded EtherNet/IP adapter facilitates seamless integration with Rockwell Automation controllers.
Another benefit is the flexible motor control options, allowing users to tailor drive performance to specific application requirements. Simplified programming and commissioning tools further streamline the setup process, reducing downtime and improving overall efficiency. The PowerFlex 525 also offers advanced diagnostic capabilities.
Built-in safety features, like Safe Torque-Off, enhance operator safety and equipment protection. Additionally, the drive’s energy-saving capabilities contribute to reduced operational costs and environmental impact. The PowerFlex 525’s adaptability and user-friendly design make it a valuable asset for diverse industrial automation applications. The drive supports multi-drive configurations.
Installation and Wiring Instructions
Users are required to familiarize themselves with all installation and wiring instructions, in addition to requirements of all applicable codes, laws, and standards before beginning.
Complying with EMC Directive
Adhering to the EMC (Electromagnetic Compatibility) Directive is crucial for the proper and safe operation of the PowerFlex 525 drive within its intended environment. This directive ensures that the drive does not generate excessive electromagnetic interference that could disrupt other nearby equipment, and that it is also immune to a reasonable level of external electromagnetic disturbances.
Refer to the PowerFlex 525 User Manual for detailed instructions on how to achieve compliance. These instructions typically involve proper grounding techniques, the use of appropriate shielded cables, and the correct installation of any necessary filters or suppression devices. Paying close attention to these guidelines will not only ensure compliance with regulatory requirements but also contribute to the overall reliability and longevity of the drive system.
Failure to comply with the EMC Directive may result in operational issues, equipment damage, and potential legal ramifications. Always consult the user manual for the most up-to-date and specific guidance.
Basic Operation and Programming
This section details fundamental operations and programming of the PowerFlex 525, including parameter settings, motor control, and basic drive functions.
Refer to the manual for comprehensive instructions and examples.
Direct Run Options
Exploring direct run options with the PowerFlex 525 drive involves understanding how to operate the drive without extensive programming or network communication.
Users often seek to manually control the drive for testing conveyor belts, troubleshooting, or simplified applications.
While the PowerFlex 525 lacks a traditional keypad interface like the PowerFlex 40, alternative methods exist for direct control.
One approach involves configuring parameters 46 and 47, potentially enabling basic run functionality via terminal inputs.
However, complete reliance on the user manual is essential, as direct run capabilities might be limited compared to servo drives with dedicated direct run functions in RSLogix 5000.
Consult the manual for precise parameter settings and safety considerations.
Understanding the specific application requirements is crucial when considering direct run options.
Evaluate whether basic start/stop control is sufficient or if more advanced control via EtherNet/IP is necessary for seamless integration with PLCs.
Remember, safety should always be a priority when manually operating the drive.
EtherNet/IP Adapter Configuration
Configuring the EtherNet/IP adapter enables seamless integration with Rockwell Automation controllers.
This involves setting up the adapter, configuring I/O messaging, and understanding implicit and explicit communication methods.
Setting up the Adapter
Configuring the PowerFlex 525’s EtherNet/IP adapter involves several key steps to ensure seamless communication within your industrial network. First, verify the physical connections, ensuring the Ethernet cable is securely connected to both the drive and the network switch or controller. Next, power up the PowerFlex 525 drive and access its configuration parameters using software like Connected Components Workbench or Studio 5000 Logix Designer. Locate the network settings, including the IP address, subnet mask, and gateway address. Assign a unique and valid IP address to the adapter, ensuring it doesn’t conflict with other devices on the network. Configure the subnet mask to match your network’s configuration, and set the gateway address if necessary for communication beyond the local subnet; Once these basic network parameters are set, save the configuration and cycle power to the drive for the changes to take effect. You can then use network diagnostic tools to verify that the PowerFlex 525 adapter is visible and communicating on the EtherNet/IP network. Proper setup is essential for reliable data exchange and control.
Configuring I/O Messaging
After successfully setting up the EtherNet/IP adapter on your PowerFlex 525, the next crucial step involves configuring I/O messaging. This process defines how data is exchanged between the drive and the controller. Begin by determining the appropriate I/O connection type: implicit or explicit messaging. Implicit messaging provides real-time, cyclic data exchange, ideal for time-critical applications. Explicit messaging allows for on-demand data transfer, suitable for infrequent parameter adjustments or diagnostics.
Within your programming software, such as Studio 5000 Logix Designer, configure the input and output assemblies. These assemblies define the data structure and the specific parameters being transmitted. Carefully map the desired drive parameters (e.g., speed reference, status words) to the corresponding controller tags. Ensure that the data types and sizes match to prevent errors. Define the Requested Packet Interval (RPI) for implicit messaging, balancing data update frequency with network bandwidth. Test the configuration by monitoring the data flow between the drive and the controller, verifying accuracy and responsiveness.
Troubleshooting Common Issues
Encountering issues with your PowerFlex 525 drive? This section provides guidance on diagnosing and resolving common problems. Start by checking the drive’s fault codes displayed on the HMI or through your programming software. Consult the user manual for a detailed description of each fault and recommended solutions. Verify the power supply to the drive, ensuring proper voltage and stable connections. Inspect all wiring connections for looseness or damage, paying close attention to motor and network cables.
If experiencing communication errors, confirm the EtherNet/IP network settings, including IP addresses and subnet masks. Use network diagnostic tools to check for connectivity issues. For motor-related problems, examine the motor windings for insulation breakdown and verify the motor’s nameplate data matches the drive’s configuration. If the drive trips frequently, investigate potential overload conditions or excessive acceleration/deceleration rates. When troubleshooting, always prioritize safety by disconnecting power before inspecting any components.
Safety Guidelines and Important User Information
Prioritize safety when working with the PowerFlex 525 drive. Always disconnect power before performing any maintenance or troubleshooting activities. Ensure qualified personnel handle installation, programming, and repairs. Adhere to all applicable codes, laws, and standards. Use appropriate personal protective equipment, such as safety glasses and gloves. Be aware of potentially hazardous voltages and currents within the drive and connected equipment. Never operate the drive with damaged or missing components.
Verify that the drive is properly grounded to prevent electrical shock. Implement lockout/tagout procedures before servicing the drive. Keep the drive enclosure clean and free from obstructions. Monitor the drive’s operating temperature to prevent overheating. Do not exceed the drive’s rated voltage or current. Ensure proper ventilation to dissipate heat effectively. Regularly inspect wiring and connections for signs of wear or damage. Replace any faulty components immediately. Consult the user manual for detailed safety information and warnings.
Accessing the User Manual
The PowerFlex 525 user manual is readily accessible through online resources and downloadable PDF files. Consult the manual for comprehensive instructions, safety guidelines, and troubleshooting tips.
Online Resources and PDF Downloads
Accessing the PowerFlex 525 user manual has never been easier, thanks to a variety of online resources and readily available PDF downloads.
For immediate access, visit the Rockwell Automation website, where you can find the most up-to-date version of the manual. The website also provides additional resources, such as FAQs, application notes, and software updates.
If you prefer a downloadable version, the user manual is available in PDF format. This allows you to save the manual to your computer or mobile device for offline access. Many third-party websites also host copies of the PowerFlex 525 user manual, but it is always recommended to download the manual from Rockwell Automation’s official website to ensure you have the correct and most current version.
The PDF version is ideal for printing, allowing you to have a physical copy of the manual for easy reference in the field.
Maintenance and Service
Ensuring the longevity and optimal performance of your PowerFlex 525 drive necessitates regular maintenance and timely service interventions.
Implementing a proactive maintenance schedule, as outlined in the user manual, is paramount. This includes routine inspections for any signs of wear, damage, or overheating. Periodically check and tighten all electrical connections to prevent loose wiring, which can lead to operational inefficiencies or safety hazards.
Clean the drive regularly to remove dust and debris, which can impede airflow and contribute to overheating. When performing maintenance or service, always disconnect the power supply to the drive and adhere to all safety guidelines.
For complex repairs or troubleshooting, consult the user manual for detailed procedures and diagrams. If you lack the necessary expertise, seek assistance from qualified professionals.
Regular maintenance can prevent costly downtime and extend the lifespan of your PowerFlex 525 drive.